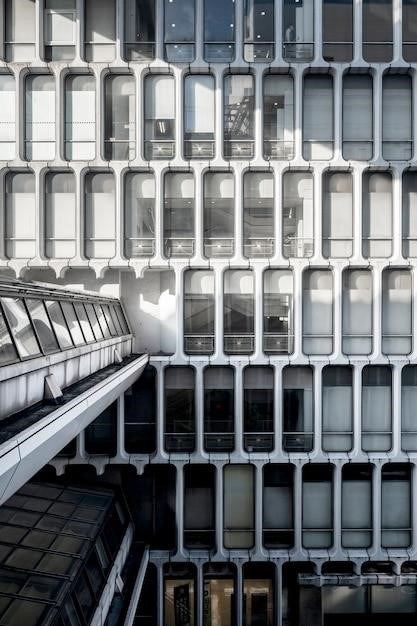
7075-T6 Aluminum Material Properties
7075-T6 aluminum is a popular and versatile alloy known for its high strength and excellent fatigue resistance, making it an ideal choice for aerospace, automotive, and structural applications. It is a heat-treatable alloy with zinc as the primary alloying element and is often used in aircraft structures, rocket components, and other demanding applications. The alloy’s mechanical and physical properties make it a valuable material for various engineering projects.
Introduction
7075-T6 aluminum is a high-strength, heat-treatable aluminum alloy renowned for its exceptional mechanical properties, making it a favored material for a wide range of engineering applications. This alloy is widely used in aerospace, automotive, and structural components where high strength, fatigue resistance, and durability are paramount. The 7075 designation refers to its specific alloy composition, with zinc being the primary alloying element. The “T6” temper designation indicates the specific heat treatment process applied to enhance the alloy’s strength and toughness. 7075-T6 aluminum exhibits excellent tensile strength, yield strength, and fatigue resistance, making it an ideal choice for demanding applications where structural integrity and reliability are critical. This comprehensive guide delves into the intricacies of 7075-T6 aluminum, exploring its material properties, applications, and considerations for its successful implementation in engineering projects.
Mechanical Properties
7075-T6 aluminum boasts a compelling set of mechanical properties that make it a standout choice for demanding applications. It exhibits high tensile strength, a measure of its ability to withstand pulling forces before breaking, typically ranging from 570 MPa (83,000 psi) to 700 MPa (100,000 psi) depending on the specific manufacturing process and heat treatment. Its yield strength, the point at which the material begins to deform permanently, is similarly impressive, commonly reaching 500 MPa (73,000 psi). Furthermore, 7075-T6 aluminum possesses exceptional fatigue resistance, allowing it to withstand repeated stress cycles without failure, which is crucial for applications like aircraft components subjected to continuous vibrations and stresses. These mechanical properties, combined with its good machinability and weldability, make 7075-T6 aluminum a versatile material for a diverse range of structural and mechanical applications.
Physical Properties
Beyond its impressive mechanical properties, 7075-T6 aluminum exhibits a range of physical characteristics that contribute to its versatility and suitability for various applications. Its density, a measure of its mass per unit volume, is relatively low at 2.81 g/cm³ (0.102 lb/cu in), making it lightweight yet strong. This combination of strength and lightness is particularly valuable in aerospace applications where weight reduction is paramount. Additionally, 7075-T6 aluminum possesses a thermal conductivity of 160 W/mK, signifying its ability to efficiently transfer heat. This property makes it suitable for applications involving heat dissipation, such as heat sinks in electronic devices. Furthermore, its electrical conductivity of 21.5 MS/m indicates its ability to conduct electricity effectively, which can be advantageous in certain electrical applications. These physical properties, combined with its excellent machinability and weldability, further enhance the versatility of 7075-T6 aluminum, making it a preferred material for a wide range of engineering projects.
Common Calculations
When working with 7075-T6 aluminum, engineers and designers often perform various calculations to determine its suitability for specific applications. These calculations typically involve determining factors like stress, strain, and deflection, which are crucial for ensuring structural integrity and performance. For example, calculating the maximum stress that a 7075-T6 aluminum component can withstand before yielding or failing is essential in structural design. This involves utilizing the material’s yield strength and applying appropriate safety factors. Similarly, calculating the strain, or deformation, that a component will experience under a given load is crucial for ensuring that it meets desired performance criteria. Moreover, determining the deflection of a component, or its change in shape under load, is important for ensuring proper functionality and avoiding potential failures. These calculations are typically performed using established engineering principles and formulas, taking into account the specific properties of 7075-T6 aluminum, such as its elastic modulus, Poisson’s ratio, and shear modulus. By meticulously performing these calculations, engineers can ensure that components made from 7075-T6 aluminum meet the required performance standards and deliver optimal results in their intended applications.
Alloy Composition
The composition of 7075-T6 aluminum is crucial to its unique properties. It’s categorized as a 7000-series aluminum alloy, characterized by its high strength and excellent fatigue resistance. The primary alloying element is zinc, with magnesium and copper contributing significantly to its mechanical characteristics. The presence of these elements creates a complex microstructure, influencing the material’s strength, ductility, and resistance to corrosion. Furthermore, the addition of smaller amounts of other elements, such as manganese, iron, and silicon, further enhances its properties. This specific alloy composition provides a balance of strength, toughness, and machinability, making it highly desirable for applications requiring high performance and reliability. The precise composition of 7075-T6 aluminum can vary depending on the manufacturer and specific application. However, the general composition typically falls within a specific range to ensure consistent performance and quality. The specific details of the alloy composition are often found in material datasheets and specifications provided by manufacturers and suppliers.
Followup Questions
Understanding the properties of 7075-T6 aluminum can lead to further inquiries about its specific applications and limitations. Some common followup questions might include⁚
What are the specific applications of 7075-T6 aluminum in aerospace and other industries?
How does the T6 tempering process affect the mechanical properties of the aluminum alloy?
What are the limitations of 7075-T6 aluminum in terms of weldability, corrosion resistance, and machinability?
Are there any alternative alloys or materials that could provide similar properties or performance?
What are the environmental considerations associated with the production and use of 7075-T6 aluminum?
By exploring these questions, you can gain a more comprehensive understanding of the advantages and disadvantages of using 7075-T6 aluminum in specific applications.
Further Reading
To delve deeper into the intricacies of 7075-T6 aluminum and its material properties, there are several valuable resources available for further reading. These resources can provide detailed information on specific aspects of the alloy, such as its microstructure, processing methods, and applications.
For a comprehensive understanding of aluminum alloys, including 7075-T6, the NASA STI Repository (also known as the NASA Technical Reports Server (NTRS)) is a highly recommended resource. It offers a vast collection of technical reports, journal articles, and other documents related to aerospace materials.
The website Matweb is another excellent source for material properties data, including detailed information on 7075-T6 aluminum. It provides a comprehensive database of materials and their properties, making it a valuable tool for engineers and researchers.
Additionally, various academic journals, such as “Materials Transactions” and “Materials Science and Engineering,” publish research articles on aluminum alloys and their properties. These articles often delve into specific aspects of 7075-T6 aluminum, providing insights into its behavior under different conditions.
Applications
The exceptional strength, fatigue resistance, and machinability of 7075-T6 aluminum make it highly sought after in various industries. Its applications span diverse fields, showcasing its versatility and ability to meet demanding requirements.
In aerospace, 7075-T6 is a mainstay material for aircraft structures, particularly in high-stress areas. Its strength-to-weight ratio makes it ideal for fuselage components, wing spars, and landing gear parts. It’s also found in rocket components, where its high fatigue resistance is crucial for withstanding the rigors of launch and flight.
Beyond aerospace, 7075-T6 finds applications in automotive, where it is used for structural components like chassis parts, suspension arms, and high-performance engine components. Its strength and durability make it suitable for demanding automotive applications, contributing to vehicle performance and safety.
The alloy’s versatility extends to general engineering applications, where it is used for tooling, dies, and other high-strength components. Its machinability allows for precise and complex shapes, making it a valuable material for manufacturing tools and components.
Advantages and Disadvantages
7075-T6 aluminum boasts a compelling set of advantages that make it a popular choice for a wide range of applications. Its high strength-to-weight ratio, excellent fatigue resistance, and good machinability contribute to its widespread use. However, it’s essential to acknowledge its drawbacks, particularly its susceptibility to corrosion and limited weldability.
The high strength-to-weight ratio of 7075-T6 is a key advantage, making it ideal for applications where weight reduction is critical, such as aerospace and automotive. This property allows for lighter structures while maintaining high strength, improving performance and fuel efficiency.
Its excellent fatigue resistance is another significant advantage, enabling it to withstand repeated stress cycles without failure; This property is crucial for components subjected to cyclic loading, like aircraft wings and landing gear.
The good machinability of 7075-T6 makes it easier to fabricate complex shapes and intricate designs, opening up possibilities for diverse applications. This property allows for precise machining and tooling, contributing to the overall quality and functionality of components.
Heat Treatment
Heat treatment plays a crucial role in achieving the desired mechanical properties of 7075-T6 aluminum. The T6 temper designation indicates a specific heat treatment process that enhances the alloy’s strength and hardness. This process involves a series of controlled heating and cooling steps designed to optimize the microstructure of the aluminum.
The first step in the T6 heat treatment process is solution heat treatment. This involves heating the aluminum to a specific temperature, typically around 930°F (500°C), and holding it for a predetermined time. This heating allows the alloying elements, such as zinc, magnesium, and copper, to dissolve into the aluminum matrix.
After solution heat treatment, the aluminum is rapidly cooled, usually by quenching in water or a specialized quenching medium. This rapid cooling prevents the dissolved alloying elements from precipitating out of the aluminum matrix.
The final step in the T6 heat treatment process is artificial aging. This involves reheating the aluminum to a lower temperature, typically around 340°F (170°C), and holding it for a specific time. This reheating allows the dissolved alloying elements to precipitate out of the aluminum matrix, forming fine particles that strengthen the alloy.
Corrosion Resistance
While 7075-T6 aluminum possesses excellent strength and fatigue resistance, its corrosion resistance is considered average. The alloy’s high zinc content contributes to its susceptibility to corrosion, particularly in environments with high humidity or exposure to saltwater.
To mitigate corrosion concerns, various surface treatments and protective coatings can be applied. Anodizing is a common technique that creates a hard, oxide layer on the aluminum surface, enhancing its corrosion resistance. Other options include chromate conversion coatings, which offer a protective barrier against corrosion.
In addition to surface treatments, careful design considerations can help minimize corrosion risks. For instance, avoiding sharp corners and crevices can reduce areas where moisture can accumulate and promote corrosion. Proper cleaning and maintenance are also essential to prevent the buildup of dirt and debris that can accelerate corrosion.
In applications where corrosion is a major concern, alternative aluminum alloys with higher corrosion resistance may be considered. However, it is important to note that these alloys might compromise some of the desirable mechanical properties of 7075-T6.
Machinability
7075-T6 aluminum is known for its good machinability, although it can be more challenging to machine than some other aluminum alloys. The alloy’s high strength and hardness can lead to increased tool wear and require higher cutting forces. However, with proper tooling and machining techniques, 7075-T6 can be machined efficiently.
Sharp cutting tools made from high-speed steel or carbide are recommended for machining 7075-T6. Cutting speeds and feed rates should be carefully optimized to minimize tool wear and ensure a good surface finish. Using cutting fluids can also help reduce tool wear and improve chip evacuation, facilitating a smoother machining process.
It is important to note that machining 7075-T6 can generate heat, which can lead to work hardening and potentially affect the material’s properties. Therefore, using appropriate cooling methods and maintaining a stable machining environment is crucial.
Welding
Welding 7075-T6 aluminum presents unique challenges due to its high strength, susceptibility to cracking, and potential for distortion. While it is not considered readily weldable, specialized techniques and procedures can be employed for successful welding.
The high strength of 7075-T6 can cause rapid cooling rates during welding, increasing the risk of hot cracking. Preheating the material before welding can help reduce these risks by slowing down the cooling process and minimizing thermal stresses. Post-weld heat treatments are often necessary to relieve stresses and improve the weld’s strength and ductility.
Gas tungsten arc welding (GTAW) and gas metal arc welding (GMAW) are commonly used for welding 7075-T6. However, careful selection of welding parameters, filler materials, and post-weld procedures is essential for achieving sound welds with acceptable mechanical properties. Specialized welding techniques, such as friction stir welding, can also be considered for joining 7075-T6 components.